It will take time, possibly around six months, before the Japanese automotive and other industries hit hard by the March 11 earthquake and tsunami will achieve a full recovery.
However, most partial operations could be resumed much sooner, as early as the start of April.
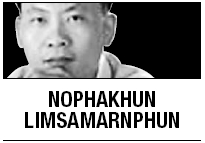
Substantial damage, especially in the northeastern part of Japan, was caused by the magnitude-9 quake and ensuing massive tsunami. As a result, major automotive companies as well as parts makers have seen their factories and equipment disabled by either the disaster itself or the subsequent power shortages.
In addition there are still evacuation warnings for factories near the Fukushima nuclear power complex due to possible radiation leaks from the damaged plant. Tokyo Electric Power also has imposed electricity supply restrictions which undoubtedly hinder the restart of industrial operations.
According to an international bank’s research, genuine recovery should start around September because of the time needed to remove bottlenecks for electronic components and other parts.
Besides, electronic components used in autos, shortages of rubber and resin-related products, metal castings, steel and nonferrous metals will contribute to production bottlenecks. Due to the shortage of power supply, round-the-clock production shifts are now not practical either.
Regarding the auto industry in Thailand, where Japanese firms are among the major players, there will be short-term negative impacts due to the shortage of some parts and components from Japan. This disruption is happening at a time when demand for locally-assembled vehicles continues to grow strongly, with production targets for both domestic and export sales projected to rise by 20 per cent from last year’s figures.
At present, imports from Japan account for 65 percent of the Thai auto industry’s overall parts imports. In addition, some locally-produced parts also need steel imported from Japan to meet the automakers’ specifications. At this stage, inventories of these raw materials are enough for another three weeks. Thereafter, new shipments from Japan could be delayed during the second quarter.
While the power supply disruption in Japan will not allow its steel and other parts factories to run at full capacity in the coming months, it is possible automakers will consider using steel from other sources such as India and Korea to avoid more serious production bottlenecks. There will be requirements for comprehensive testing, so this will also take time.
On a positive note, another international bank’s research says production and sales targets in Thailand’s domestic and export markets are still relatively strong. In addition, it is likely that the Japanese auto industry will further diversify production risks out of Japan in the wake of the crises.
This means there could be new investment in the auto and parts industry in Thailand and other ASEAN countries as the ASEAN Economic Community becomes effective in 2015, creating a combined market of more than 580 million consumers, where most import tariffs will be zero.
Thailand and other ASEAN countries are also positioned as a single production base that can tap demand within the 10-country regional grouping and other global markets.
The Thai auto industry is the largest in ASEAN with a combined production capacity of more than 1.4 million units. About half of the output is sold domestically while the other half is exported. Further investment will help lower unit production costs, thus boosting the price competitiveness of vehicles sold in domestic and overseas markets.
By Nophakhun Limsamarnphun
Nophakhun Limsamarnphun is a columnist of the Nation, a Bangkok-based Thai daily. ― Ed.
(The Nation/Asia News Network)