LIEPZIG, Germany ― Four massive wind turbines stand near BMW’s Leipzig plant, whipping up energy to help power the production of the 1 Series vehicles and the i3, the carmaker’s first electric car.
The turbines ― capable of generating 26,000 megawatt hours per year ― are part of BMW’s ambitious i project that aims to build possibly the world’s most sustainable car in the most environment-friendly way.
“Production defines the i3 car,” said Jochen Muller, a corporate communications manager of BMW Group, revealing some of the secrets of the battery-powered i3 hatchback to a group of journalists last week.
Carbon-fiber is the key to the i3 four-door compact, which will start rolling off the assembly line at the plant in the eastern German city late this year.
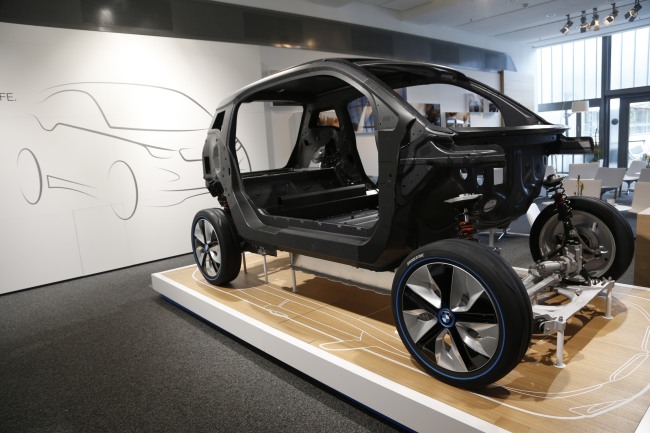 |
No conveyors, no welding. The carbon fiber body of the BMW i3 on show at the Leipzig plant. ( BMW Group) |
The finished car will weigh just 1,250 kilograms, including the 230-kilogram battery pack. This means the i3’s agility and range will far advance its heavier rivals such as the Nissan Leaf (1,565 kilograms) and the Renault Fluence or SM3 ZE in Korea (1,605 kilograms).
BMW’s uses lightweight materials to compensate for the extra weight of the battery ― Korea’s Samsung SDI is the exclusive battery supplier ― including carbon fiber-reinforced plastic commonly used in motor racing or supercar manufacturing.
BMW established a joint venture with U.S. carbon specialist SGL Automotive Carbon Fibers, and the preformed carbon-fiber mats arrive at the Leipzig factory and each car body consists of nine preformed panels.
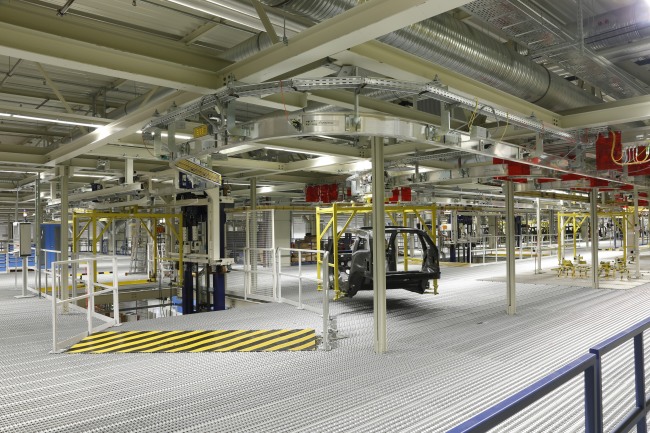 |
A concept BMW i3 is displayed at the Leipzig plant in Germany. (BMW Group) |
The body is assembled entirely by robots ― 160 of them ― using polyurethane glue to mount the panels on a rolling aluminum chassis.
There are no conveyors or welding, as use of carbon fiber eliminates the press shop and the paint shop.
Carbon fiber is also cheaper to repair, the carmaker said, explaining that costs go down by 10 to 20 percent, while labor time also falls by 10 to 15 percent.
The car is expected to go from 0 to 100 kilometers per hour in less than 8 seconds. Its top speed will be limited to 150 kilometers per hour.
The fully-charged lithium-ion battery under the floor can deliver an all-electric range of 160 kilometers. For customers who want to drive longer distances, BMW will offer an optional extender that increases the range to 320 kilometers.
“After evaluating more than 20 million kilometers driven by our test customers with Mini E and BMW ActiveE electric cars, we found about 90 percent of daily commutes are (within) around 45 kilometers in mega cities,” said the BMW manager.
The carmaker said 25 percent of the materials used in the i3 interior and 25 percent of the thermoplastics are recycled or are made from renewable resources. And 80 percent of aluminum parts are produced using clean energy or are made from recycled aluminum.
“The i3 is reinventing BMW to have the right solutions for sustainable mobility,” said Glenn Schmidt, BMW Group’s head of steering government affairs, in his recent visit to Seoul when the carmaker and the Environment Ministry held a conference on E-mobility.
He predicted the i3 would appeal to typical BMW customers as well as people with a certain level of awareness about environment sustainability.
“It is still BMW and still fun to drive. Our customers are always open to trying new technologies,” he said.
The price is inevitably a drawback for the BMW’s first electric car whose European price tag is 40,000 euro ($36,000). The BMW executive, however, hinted that the international price, including in Korea, would be less than expected.
By Lee Ji-yoon, Korea Herald correspondent
(
jylee@heraldcorp.com)