The first batch of COVID-19 vaccines may arrive here in the coming weeks, as President Moon Jae-in on Monday announced the launch in February of the nationwide vaccination campaign.
When it comes to the jab itself, South Korea says it has secured more than enough vaccine to inoculate its 51.6 million population. The question now is whether the country can handle all the logistical challenges required to take vaccines from the factory floor to patients’ arms.
To administer the shots as quickly and safely as possible, meticulous planning, coordination and monitoring are essential, with the backing of related industries and infrastructure for the supply, storage and delivery of the precious shots.
What is needed?
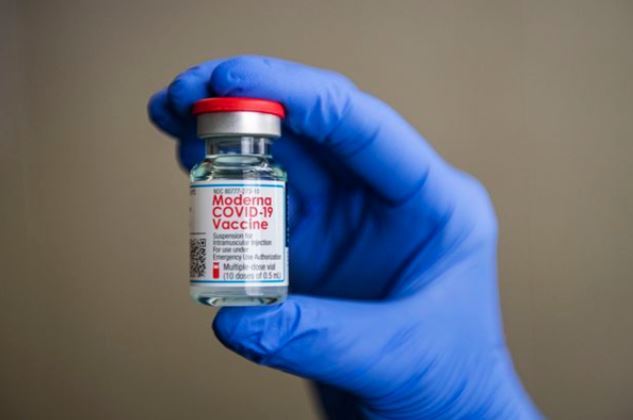 |
Moderna’s mRNA vaccine is expected to be available in Korea in May. (Reuters-Yonhap) |
The requirements depend on the characteristics of the vaccine -- how it is administered and what it requires in terms of transportation and storage.
Korea will get more than 100 million doses of vaccines through five deals -- 20 million doses each from the global vaccine procurement facility called COVAX, AstraZeneca and Pfizer-BioNTech; 40 million doses from Moderna; and 6 million doses from Janssen. The government was close to striking a sixth deal to purchase another 10 million doses from US drugmaker Novavax, local reports said Tuesday.
The first shots to arrive will likely be the COVAX vaccines, according to Korea’s Disease Control and Prevention Agency. The COVAX facility offers a mixture of vaccines, comprising those from Pfizer, AstraZeneca, Janssen, Sanofi-GSK and Novavax. Some of these vaccines are still under development. As of Tuesday, the government was uncertain which one it would get or the precise timing of plans to supply it.
Putting COVAX aside, the next vaccine to be available in Korea will be from AstraZeneca. AstraZeneca vaccines have the advantage of being contract-manufactured by a local vaccine maker, SK Bioscience.
SK Bioscience and AstraZeneca applied for the Korean Drug Ministry’s approval for the use of the vaccine on Jan. 4, both for the bulk produced in Korea and for the bulk to be transported across the ocean. As the ministry vowed to make its decision within 40 days, the AstraZeneca vaccine is anticipated to be available from February.
Janssen vaccines will likely enter Korea in the second quarter, Moderna vaccines in May and Pfizer vaccines in the third quarter, according to the Korean authorities.
Pfizer, Moderna and AstraZeneca vaccines need to be administered twice, weeks apart. Janssen’s, still under development, comes in a single shot.
Of the three, Pfizer’s messenger RNA (mRNA) vaccine is the trickiest to handle, as it needs to be stored and transported at minus 70 degrees Celsius. AstraZeneca’s vaccine requires mere refrigeration, while Moderna’s and Janssen’s need a cold chain of minus 20 degrees Celsius.
Transporting the vaccines will require large amounts of dry ice and a temperature-controlled transportation system -- including on the plane.
Pfizer ships the shots in thermal containers filled with dry ice that can maintain the optimal temperature for 10 days. Once they arrive, it is up to Korea to decide what to do. It can either use Pfizer’s thermal containers, refilling them with dry ice every five days for up to 30 days of storage, or put the unopened containers in superfreezers to extend the shelf life to six months. Once thawed and kept in a normal refrigerator at 2 to 8 degrees Celsius, the vaccine is good for just five days.
Airlines say ‘ready for the mission’
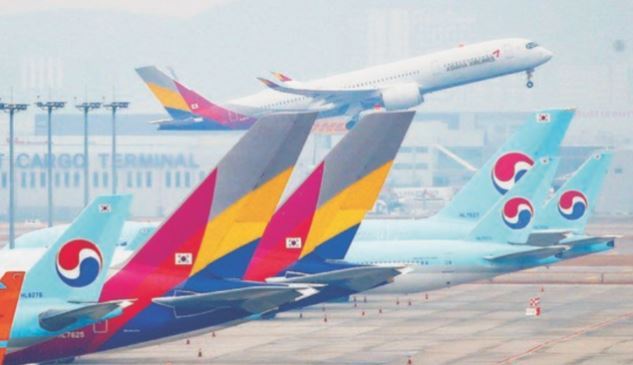 |
Korean Air and Asiana Airlines (Yonhap) |
Korea’s two national flag carriers, Korean Air and Asiana Airlines, say they have the required infrastructure in place to deliver COVID-19 vaccines, including Pfizer’s.
Both airlines have established a task force dedicated to vaccine delivery and obtained CEIV Certification -- a standard set by the International Air Transport Association to safely transport temperature-controlled and time-sensitive products, including vaccines.
“To deal with the increase in cargo volumes as a result of coronavirus vaccines, we have formed a task force and have successfully transported raw materials (used to make COVID-19 vaccine),” said one official at Korean Air.
Korean Air has experience delivering medicine and fresh goods, which accounted for 10 percent of its cargo volume last year.
The company has refrigeration facilities that can accommodate up to 100 tons of cargo at its cargo terminal at Incheon Airport, with plans to set up a cool cargo center sometime this year for vaccine delivery.
And in December, in a country first, the airline transported raw materials used to make COVID-19 vaccine from Korea to the Netherlands.
Asiana Airlines, for its part, has teamed up with special container manufacturers to establish a cold chain system with a fleet of 12 cargo aircraft on standby, once vaccine rollout begins in the country. In late December it successfully handled the shipment to Moscow of a batch of Russia’s Sputnik V vaccines produced in Korea.
Ground players wish to win honor of vaccine delivery
 |
A Yongma Logis employee loads pharmaceuticals into a temperature-controlled warehouse at the company’s Anseong center. (Yongma Logis) |
Once unloaded, the vaccines must go through a cold network to reach dosing stations across the country, from warehouses to special delivery trucks.
Korea SuperFreeze is a notable player in the field of cold storage, as it is currently the only operator of ultra-low-temperature warehouses.
Located in Pyeongtaek, Gyeonggi Province, the company uses liquefied natural gas as cold as minus 162 degrees Celsius to create a storage environment between minus 70 and minus 85 degrees Celsius.
A Korea SuperFreeze official told The Korea Herald that it had received inquiries from government authorities, but that no contract had been struck as of Monday.
“We have two minus 60 degrees Celsius rooms and one minus 80 degrees Celsius room,” the official said. “Should a deal materialize, we plan to combine these rooms and operate the total 1,600-square-meter storage space at minus 70 degrees Celsius.”
It is not just conventional logistics companies that are rising to meet the call of the times. A drugmaker called Icure Pharm even changed its corporate mandate in December to add a new business purpose -- the import and distribution of vaccines -- in order to deliver the precious shots.
Faced with new competition, existing logistics firms are revamping their systems to appeal to the government.
Yongma Logis, a Dong-a Socio logistics company, said Monday that it has established a shipping system for pharmaceutical goods and even vaccines that need minus 20 to minus 70 degrees Celsius temperature control.
“While we do not have any deals signed, we have the capability, should our service be required,” a Dong-a Socio official told The Korea Herald.
Yongma Logis’ operations as of now can handle cargo with 1 to 30 degrees Celsius requirements. But with the help of special containers, it can carry Moderna and Pfizer vaccines at the required temperatures, the company said.
The system abides by the Ministry of Food and Drug Safety’s standards for pharmaceutical storage temperature guidelines, it said.
Yongma Logis runs a hub center in Anseong, Gyeonggi Province, where pharmaceuticals are stored and sorted for distribution to the company’s 33 distribution centers and 34 delivery centers. From there, the bundles are transported to individual hospitals and pharmacies.
The Anseong hub can maintain temperatures of 1 to 30 degrees Celsius, and has recently added a tight-seal facility that blocks external air, in an industry first, a Yongma Logis official said.
The Pfizer vaccine would be well-stored at the Anseong hub if kept inside ultra-low-temperature cooler containers, the official stressed.
“There are a number of businesses that can locally produce such containers,” the Dong-a Socio official said. “These containers may use dry ice or LNG, for which Yongma Logis will outsource to wider local suppliers.”
The whole process is run by a standardized quality-control process, wherein a quality-control team records real-time data on the shipment via automatic temperature monitoring systems.
Yongma Logis stressed that it is able to maintain the necessary temperature at all steps of the logistics process.
Ilyang Pharm Logis, another pharmaceuticals transportation company often quoted in Korean media, said in a phone conversation with The Korea Herald that it had no capacity to handle COVID-19 vaccines.
Insulation materials key for cold chain
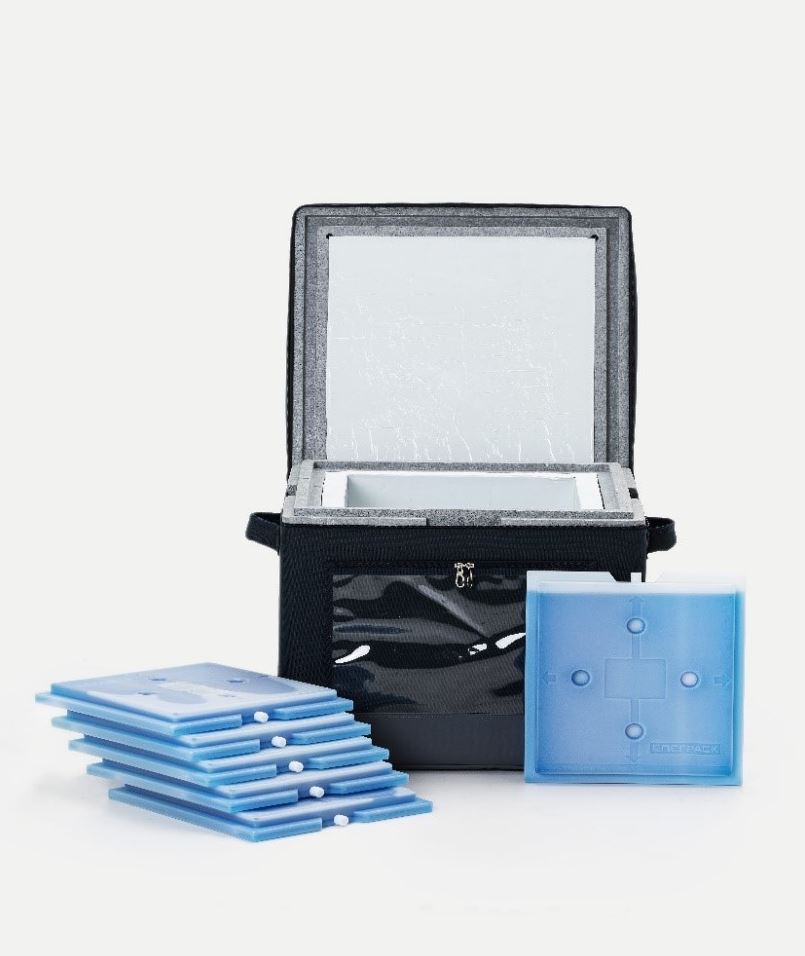 |
OCI’s icebox can maintain a temperature of minus 70 degrees Celsius for up to 250 hours. A smart “freezer container” using OCI’s Enervac insulation panels is used in extreme regions, including Antarctica. (OCI) |
As insulation materials emerge as a key element of the cold chain process, local insulator manufacturers are anticipating a strong bump in business.
According to Korean chemical company OCI, demand has spiked recently for its insulation panel Enervac, used for containers in extreme regions including Antarctica.
“The revenue of Enervac panels is expected to increase more than 200 percent on-year, with sales projected to surge in the second half of this year when COVID-19 vaccines and treatments will be deployed in full capacity (globally),” an OCI official said.
The official further added that OCI is mostly exporting the Enervac panels, as the development for currently available COVID-19 vaccines has been conducted by the US and European pharmaceutical companies.
Enervac panels, made of a raw material called fumed silica, exhibit insulation performance as much as eight times greater than that of typical insulation panels made of conventional materials such as glass wool and Styrofoam, according to OCI.
OCI’s annual production capacity of Enervac panels is 1.16 million square meters, enough for 20,000 containers, or 2 million vaccine boxes, which can transport 300 million vials of vaccines. OCI also produces its own fumed silica, with an annual production capacity of 15,000 metric tons per year.
Enervac panels are currently mounted on the prototypes of “freezer containers” developed by the Korea Railroad Research Institute. The prototypes, which are currently used in Antarctica for the stable transportation and storage of food supplies and research equipment, can maintain a temperature as low as minus 20 degrees Celsius with a built-in battery. They can operate for 72 hours at 7 degrees Celsius.
“With OCI’s independently developed Phase Change Material technology, which minimizes the container being influenced by exterior temperature fluctuations, Enervac containers can accommodate different vaccines that need to be transported at minus 70 degrees Celsius, minus 20 degrees Celsius, and from 2 to 8 degrees Celsius,” the official added.
The application of Enervac panels extends not only to containers, but also to iceboxes.
OCI’s vacuum iceboxes, with the help of dry ice, can maintain minus 70 degrees Celsius for up to 250 hours, or a little over 10 days, allowing safe storage of vaccines without additional investment in related equipment or facilities.
A point to note is that the dry ice supply may not be catching up with the rising demand.
Korean dry ice company Taekyung Chemical experienced a 200 percent rise in its stock value in 2020 on the back of increased online purchases of fresh food and the anticipation of COVID-19 vaccine needs. According to Taekyung Chemical’s half-year business report in 2019, the company’s dry ice price rose from 484 won to 550 won per kilogram due to its scarcity.
An official from Taekyung Chemical, however, told The Korea Herald that its manufacturing output has not increased correspondingly.
Dry ice is made by compressing the carbon generated in the process of creating ethanol. Carbon is the byproduct when a petroleum chemical company makes plastic products, or when an oil company purifies crude oil. The irony here is that while the demand for dry ice rose, the demand for crude oil fell inversely.
Industry insiders think the dry ice supply could be increased through increased production of crude oil.
Monitoring vaccine transportation
Just as important as physical transportation of the vaccines is a software system that will safeguard every step of the process. Samsung SDS’ cold chain monitoring system may provide a solution here -- the information technology arm of Samsung has conducted an experiment with Korea SuperFreeze and Yongma Logis, in which they ran a mock operation of transporting vaccines imported from overseas to a distribution center and then to nationwide dosing centers.
Samsung SDS is working on a pilot business model that uses blockchain technology to keep tabs on pharmaceutical deliveries.
While no concrete business plan has come out of this test run, Samsung SDS says that should the government issue a relevant plan, they would have no problem in delivering seamless service.
“There were no aspects that required reinforcements in our technology,” a Samsung SDS official told The Korea Herald. The company has years of experience in constructing software infrastructure for Samsung affiliates. It also has been running a cold chain monitoring system for high-value-added items such as wine, fresh food and chemical products for a number of years, the official said.
“We are not at the point of setting up a business for COVID-19 vaccine transportation; however, we will consider it should a need arise,” said the Samsung SDS official.
Syringes and needles
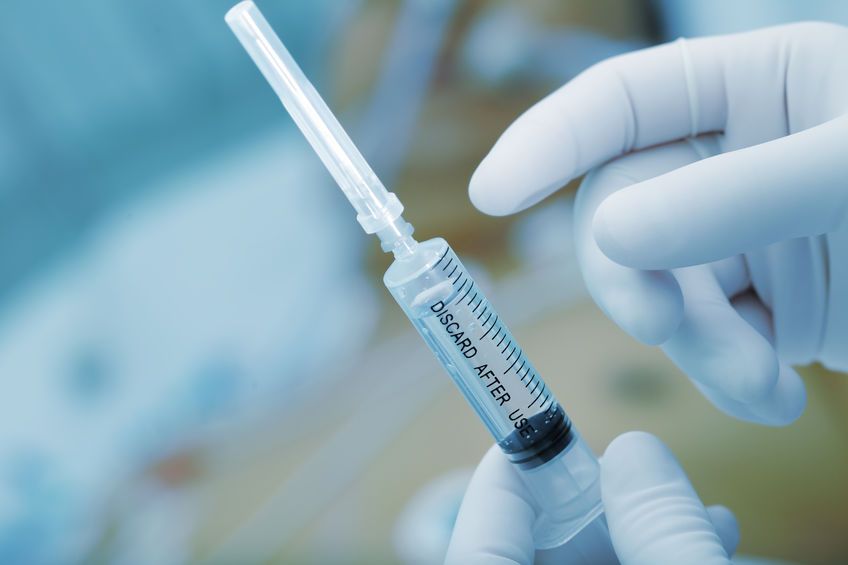 |
Syringe (123rf) |
Essential medical supplies for a vaccination program include syringes, needles and sterile alcohol prep pads.
Initially, there were fears globally that a shortage of vials, syringes and needles could delay the vaccination drive, but local manufacturers say that step-by-step preparation in coordination with the authorities will prevent that from happening in Korea.
Korean syringe manufacturers The Korea Herald has spoken to said they were more than ready to meet the demand, should the government let them know early enough what types of syringes they may require.
The frigid temperatures the mRNA vaccines are stored at do not affect them, as the vaccines will be at regular temperatures by the time they are moved to syringes for injection.
According to an official from Sungshim Medical, “If the government orders the mass production of typical medical syringes widely used in hospitals, manufacturers will be able to meet the extra demand by ramping up production.”
So the coast is clear for AstraZeneca’s vaccine.
However, if the government wants a new, specific type of syringe with different properties and a different structural design, immediate mass production may be difficult to achieve, said the official, expressing impatience that authorities still had not made a decision.
By Lim Jeong-yeo, Yim Hyun-su, Kim Byung-wook (
kaylalim@heraldcorp.com), (hyunsu@heraldcorp.com), (
kbw@heraldcorp.com)