A paradigm shift is taking place in the Korean manufacturing sector as conglomerates are increasingly embracing smart manufacturing with the goal of improving production efficiency and reducing risks using technologies of artificial intelligence, big data and internet of things, according to the patent office on Tuesday.
Smart manufacturing is artificial production processing with the goal of optimizing concept generation, production, and product transaction via the use of the latest information and communication technologies.
The Korean Intellectual Property Office said the number of related patents filed in Korea has grown fast since 2016 when the concept of smart manufacturing was first adopted here.
The number of patents filed was less than 10 from 2011 to 2014, but the figure surged to 89 in 2016, was 57 in 2017 and 52 this year until September, according to the KIPO.
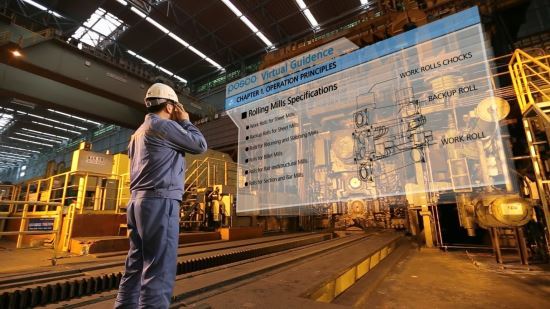 |
Posco |
The patents filed are related to sensors in manufacturing devices to collect processing data as well as big data technologies that analyze massive data real-time. The largest number of patents filed was related to control systems, which stood at 50 patents from 2011 to this year, followed by big data technologies with 47 patents and the internet of things with 18 percent, the KIPO said.
“Smart factory, which is a combination of information and communication technology and manufacturing, has a high potential growth in the era of the fourth industrial revolution. It is important for companies to establish patent strategies by connecting their business models and products in order to have an upper hand in the market,” said Jeon Il-yong, chief of the KIPO’s robotic automation screening division.
Korean tech giants, including Samsung SDS, LG CNS, SK C&C and Posco ICT, are also accelerating their smart manufacturing businesses using capabilities they gained by providing information technology services.
In August, Samsung SDS introduced its smart factory platform Nextplant, which manages the entire process of manufacturing from planning, designing, production, quality management, operation and cooperation with AI, IoT, big data and cloud technologies.
Nextplant collects and analyzes big data through IoT sensors and predicts errors to improve processing quality, the company said.
“Growing competition in the manufacturing industry allows massive data to be accumulated in the sites. We are paying attention to how to intellectualize all the manufacturing process by using the massive data,” said Samsung SDS CEO Hong Won-pyo during a media briefing in August.
Samsung SDS has applied its intelligent factory technologies to Samsung Electronics, Samsung Electro-mechanics, Samsung Display, Hyundai Mobis, Posco, Doosan Infracore and Amorepacific.
LG CNS also launched its smart factory platform Factova in April with the goal of upgrading factory automation using technologies such as IoT, cloud, big data, mobile and AI. Using Factova, companies can shorten the period of the entire manufacturing process from market research to the production of prototype from six month to two to three months, the firm said.
The platform has been applied to LG Electronics’ washing machine factory in North America, LG Display’s OLED factory and LG Chem’s battery plants in Poland. The firm plans to expand adoption to other LG affiliates’ factories.
Last year, Posco ICT also established smart factory PosFrame that applies AI technologies to production processing with the aim of realizing non-error processing and minimizing defective products. This reduces the waste of energy and establishes safe production environment by discovering risk factors at the sites in real-time, the firm said.
In February, it partnered with General Electric to jointly develop hybrid smart factory platforms by combining Posco’s PosFrame and GE’s asset performance management.
“Posco plans to establish smart factory plants into Posco’s key affiliates, including Posco Engineering & Construction, Posco Energy, Posco ICT and actively discover smart solution business in the entire group,” said a Posco spokesperson.
By Shin Ji-hye (
shinjh@heraldcorp.com)