GWANGJU ― With the launch of LG Electronics’ new flagship smartphone G4 just around the corner on April 29, the Seoul-based tech giant is carrying out a full-fledged effort to make the handset available for global customers on time.
The production facilities of LG Innotek in Gwangju, where the company manufactures camera modules for the LG handset is also in full swing to meet the deadline.
LG Group’s camera module business wing hoped that the industry’s most advanced smartphone camera of the G4 would be able to help the upcoming marquee phone to become a game changer in the global smartphone market, appealing to the so-called “selfie generation,” a term which depicts those obsessed with taking selfies.
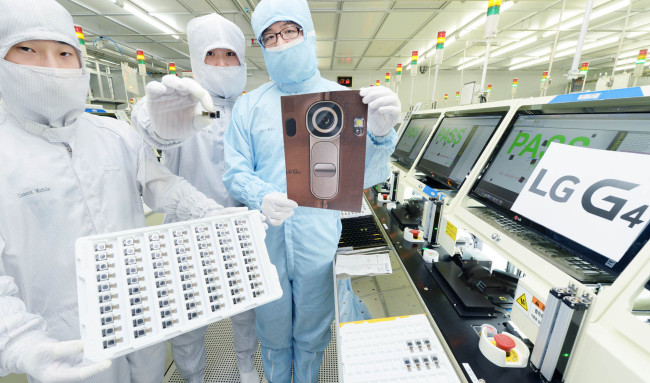 |
LG Innotek workers pose with a sheet of 16-megapixel camera modules, which will be used in LG Electronics’ new marquee smartphone G4. (LG Electronics) |
“The overall quality of the camera modules for the G4 improved more than 50 percent than that of the proceeding ones and the new products also have a 50 percent better energy efficiency,” Choi Hyung-shin, senior manager of LG Innotek’s optical solution team, told reporters visiting LG Innotek’s Gwangju plant last Friday.
The 16-megapixel rear-facing camera boasts the industry’s widest aperture setting, at F1.8, beating the F 1.9 on Samsung Electronics’ Galaxy S6 and S6 Edge and Cupertino-based Apple’s iPhone 6 and 6 Plus’ F2.2 lens.
G4 users will be able take clear pictures in any light conditions, and the 8MP front camera ― the first of its kind in the domestic market ― will allow the users to take high-resolution selfies, he added.
At LG Innotek’s Gwangju plant, the camera modules for the G4 are put to a series of reliability and durability tests after the production processes to ensure the quality.
The four-stage reliability tests take place in strictly controlled clean rooms, which do not permit more than 10 particles of 0.5 micrometers across or more per cubic foot (350 particles per cubic meter).
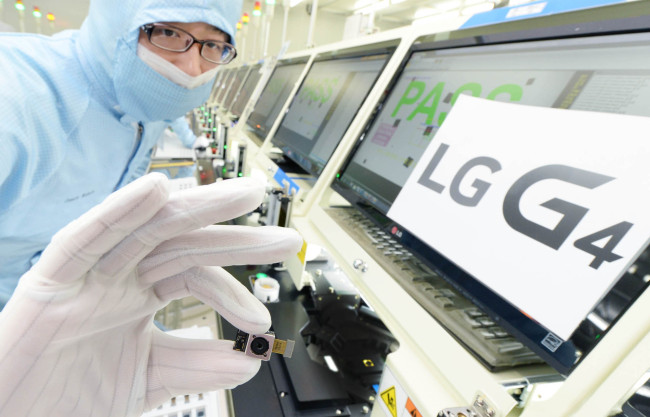
The reliability tests include color calibration tests which assesses color accuracy, and checks on anti-blur functions.
Some sample modules, then, are put into small chambers at another facility for durability tests. Inside the chambers they are tossed around or dropped from a 2-meter height. The camera modules, no larger than a thumb nail, are also placed in dust test chambers full of fine particles or temperature-humidity test chambers where the inside temperature hovers above 40 degrees Celsius with a humidity level standing at more than 120 percent.
“The tests are aimed at making sure that the cameras function properly in any environment ― both hot and cold, or more extremely put, in the Arctic and Antarctica ― and withstand exterior impacts,” said a manager of the firm’s test team.
It takes 2 1/2 days to complete the production processes and the tests, according to LG Innotek.
After the tests the camera modules are delivered to the plants in Pyeongtaek, Gyeonggi Province, for the final assembly process.
By Kim Young-won (
wone0102@heraldcorp.com)